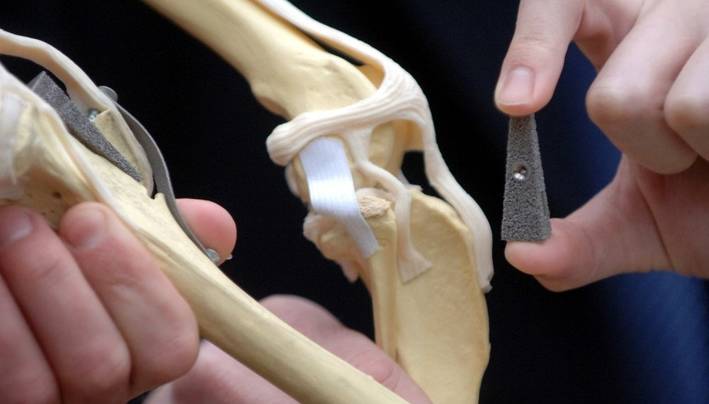
產品設計vs結構強度
產品設計除了要考慮功能與外觀,材料性質和幾何設計所構成的結構強度考量也是不可少的,因為它直接影響產品的耐用性和可靠度。不少產品在達到基本設計需求後,會更進一步希望能夠減低製造成本,典型常見的例子就是減重,希望以同樣的幾何外型,改以不同的材料來製造,這時候不但牽涉製程的改變,也必須考量到是否換了更輕、更便宜的材料後,產品仍然能夠維持在可接受的強度範圍。
複材和加入纖維補強
複合材料在設計產品上的應用,就是這種概念典型的例子,希望保有原來的強度,但是產品可以更輕盈,像是飛機、自行車架、油管等工業產品。另外一種加強結構的方式,就是在材料內加入纖維材料,像是不少電子產品的塑膠材料外殼,便常加入纖維材料(例如玻璃纖維)來增加結構強度。這樣的設計概念,當然也可以應用到生醫產品上,相較於工業產品不同的是,生醫產品更有機會面對到「客製化」設計生產的需求,例如專為新生兒設計的導管,要小巧、要輕盈、要尺寸精確,功能和結構強度也要顧及;另一項則是「仿生」(biomimic)產品的設計,例如列印出一塊仿真骨頭的材料做為手術時補骨用,這些一直是近年來3D列印在生物醫學應用上,不斷創造驚喜的一部份。
局部精準材料調校
講到產品設計結構強度的設計考量,在轉角、挖洞和某些特定曲線部位需要特別加強強度,那麼我們有辦法針對局部以纖維來加強強度嗎?在產品很小又需要精準客製化的時候,3D列印技術能做得到嗎?簡言之,在3D列印客製化醫材的同時,什麼樣的技術能把補強結構用的纖維材料,按照所需的排列方式加入指定的部位?
磁場控制纖維方向
美國麻州「東北大學」(Northeastern University)的研究員,嘗試開發出以磁場來控制這些纖維物質方向性的技術,期望在3D列印過程中能加入纖維補強結構強度,在精準控制纖維方向性這方面,已經有別於其它現有的複合材料列印技術了。首先,研究員在「陶瓷纖維」(ceramic fiber)中灑入「氧化鐵」,它是一種已經通過美國食品及藥物管理局(FDA)核准,可用來做為藥物傳輸的材料;接下來將陶瓷纖維沉浸在液態塑膠內,個別地給予超小磁場,控制纖維的方向;在3D列印的光固化成形方式下,應用電腦控制雷射光束來固化塑膠料,一層層列印,堆疊出所需產品。6吋x6吋的面積大約花費一分鐘的時間完成。
目前這項技術正積極應用於列印新生兒用的導管,另外,以「磷酸鈣」纖維(磷酸鈣為骨頭的主要組成成份)和具有生物相容性的塑膠材料來設計製造手術植入物也是未來的應用方向。
文章參考:Northeastern University
圖片來源:andreaskofner@Flickr CC BY-SA 2.0
原文參考:nature communication